Yesterday we discovered, that spring is near and work needs to be accelerated to get the boat done. Thus, from now on we will try to do longer days on Friday, Saturday and Sunday, with emphasis on the last two. Both lower planks are on, stringer notches have been completed, port stringers beveled and sanded. Joosep has been sweating epoxy on planking, so in theory, we have the port planking covered. He also finished building our first fore buoyancy compartment, complete with paint, our new foam filler, Styrofoam and epoxy. The “room” between the buoyancy and cabin got a double floor too. The canopy has been completely glassed: next is test fitting windows. Lets have the 1000 words:
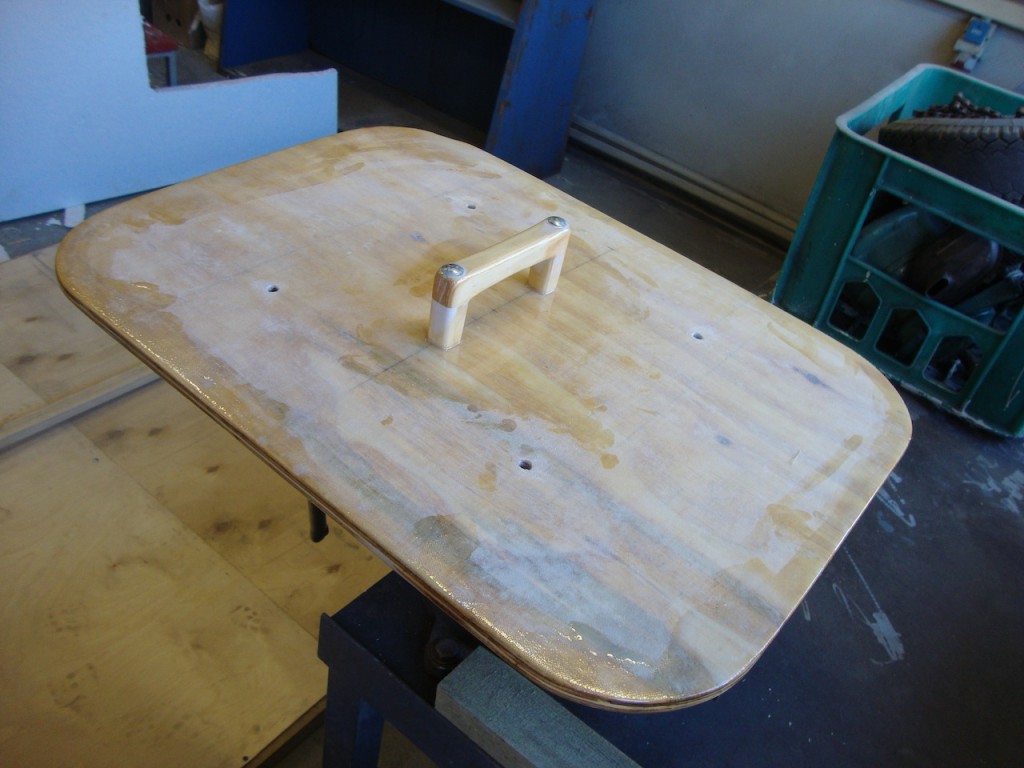
The sweetheart of Uku: watertight door for the fore compartment. Note the the luxurious handle. Both sides glassed. The four holes are for locking nuts, more on that in later posts. I have the greatest plans for painting and finishing this lovely novelty. Thanks to Doug Jackson for inspiration! His watertight doors for SV Seeker really are a piece of art.
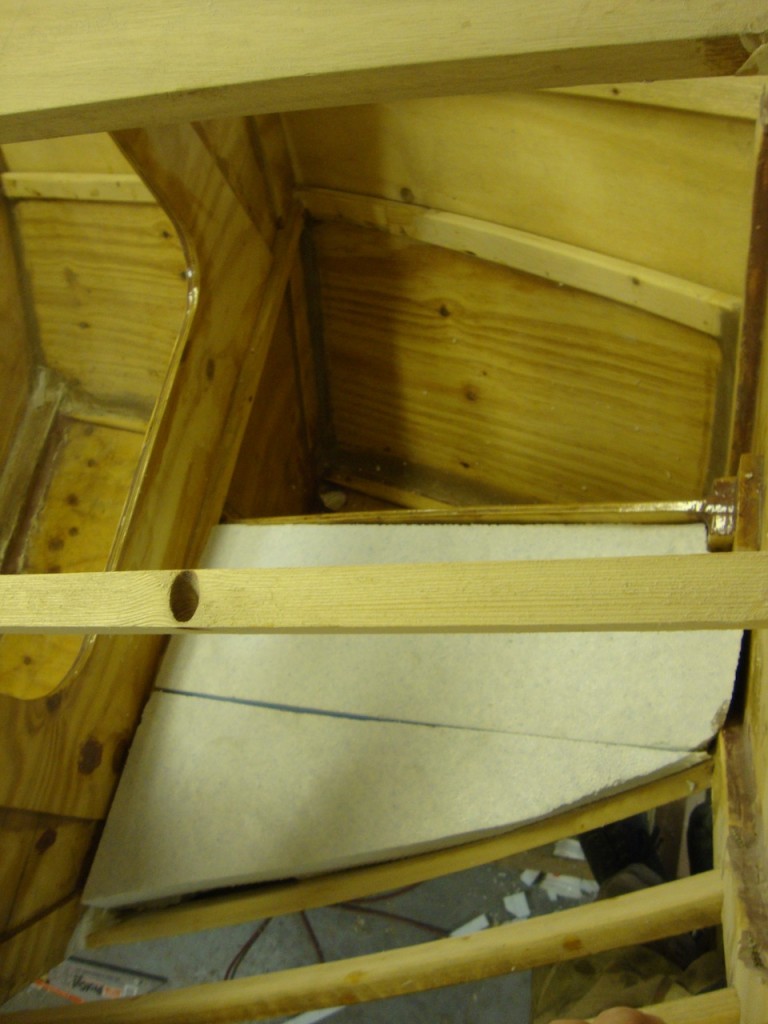
A shot of the fore buoyancy compartment. Later to be filled with foam, Styrofoam and epoxy, topped off with a plywood seal.
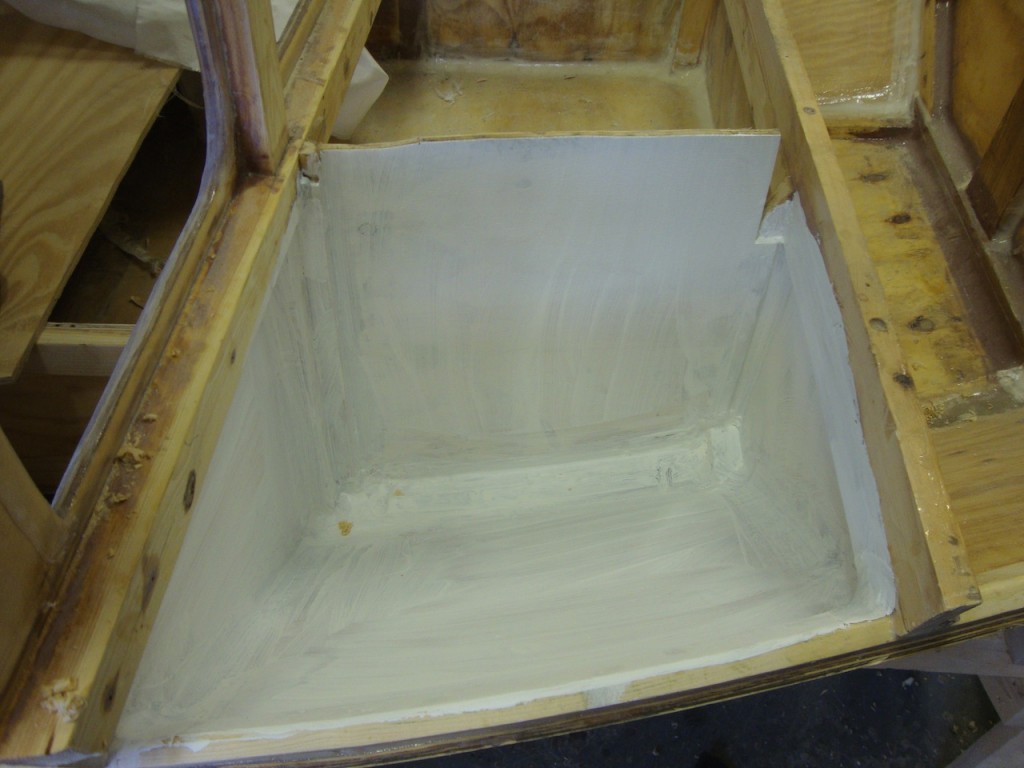
This is what our initial painting looks like: the aft buoyancy compartments on either side of the footwell, below aft shelves. This is a water based paint, simple, but more is not needed. Underneath is epoxy and glass. Two coats of paint.
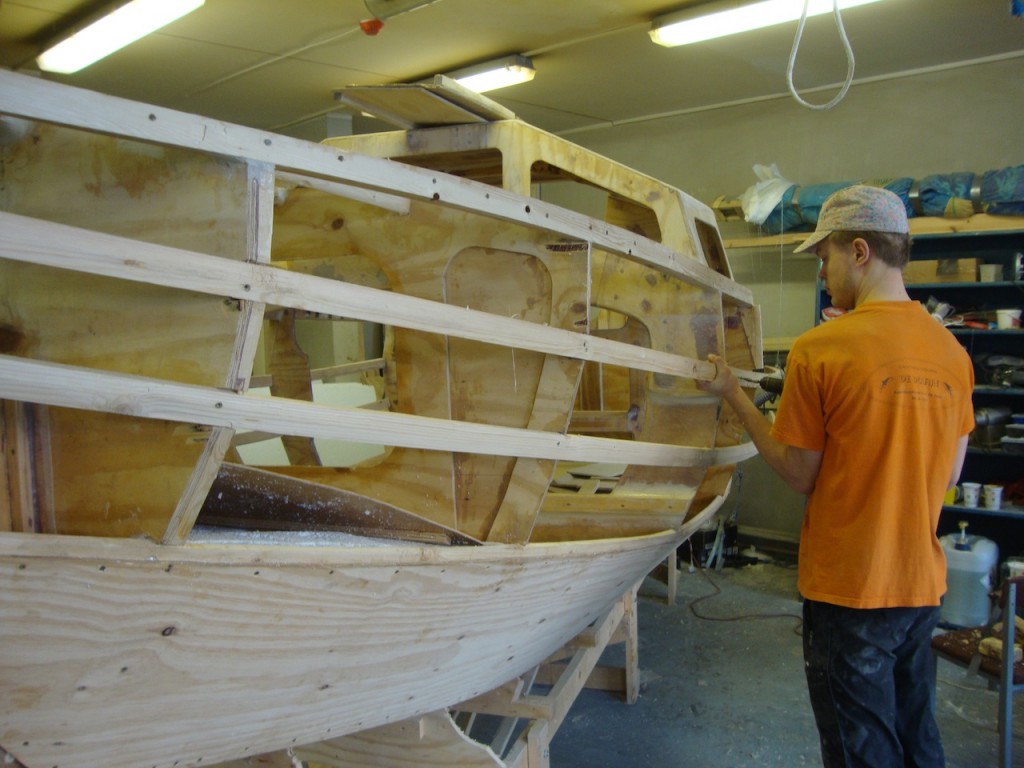
Uku taking off the beveled stringers. It took some time and a sharp plane to complete the job. It was difficult for Joosep to work on the inside with the stringers on both sides, rather acrobatic and frustrating.
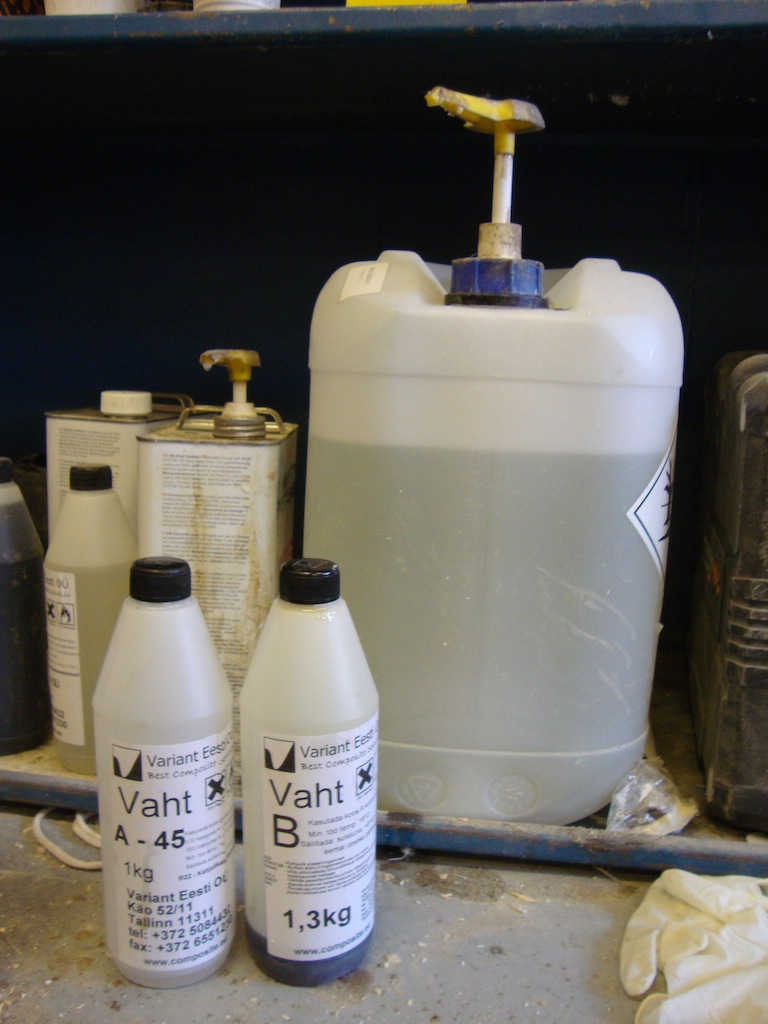
Fresh investments: a new 30 kg patch of West System epoxy resin. In total, we have bought 60 kg. In the foreground are the component “A” and “B” of the expanding filler foam. Experiments need to be done, as our initial mixes have resulted in a somewhat brittle foam, which crumples up like sand when pinched. Too bad that component “A” and component “B” do not have dispensing pumps like the larger brother in the back.
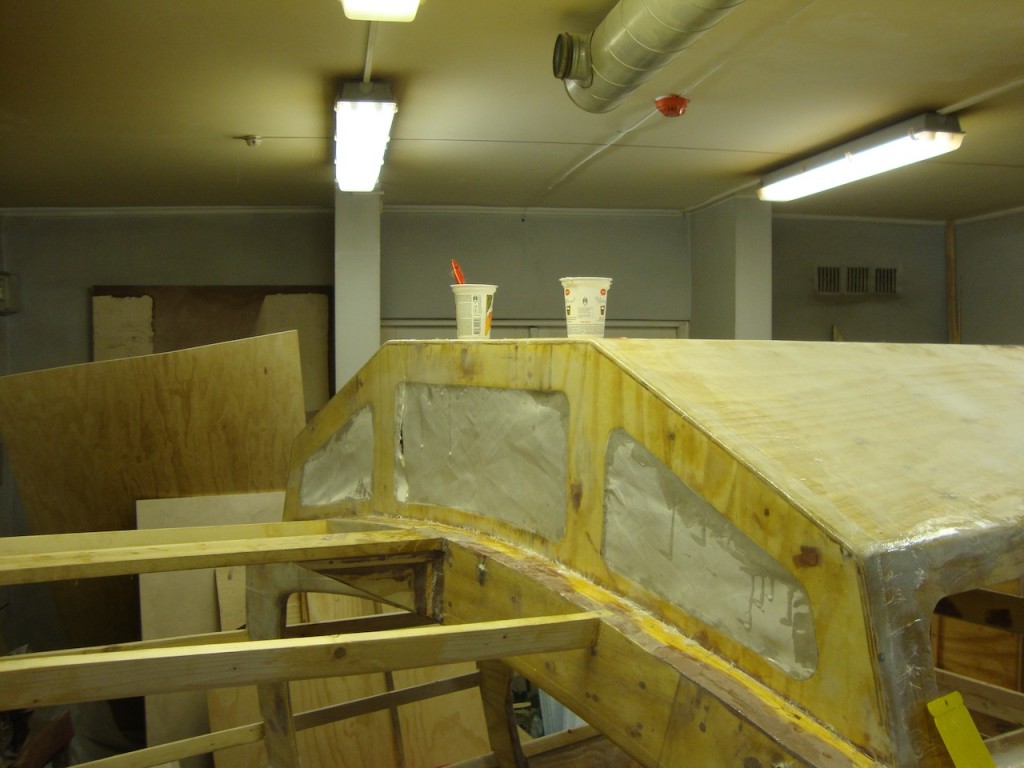
Not really the latest fashion finish on the windows: last bit of glassworks on the outside of the cabin.
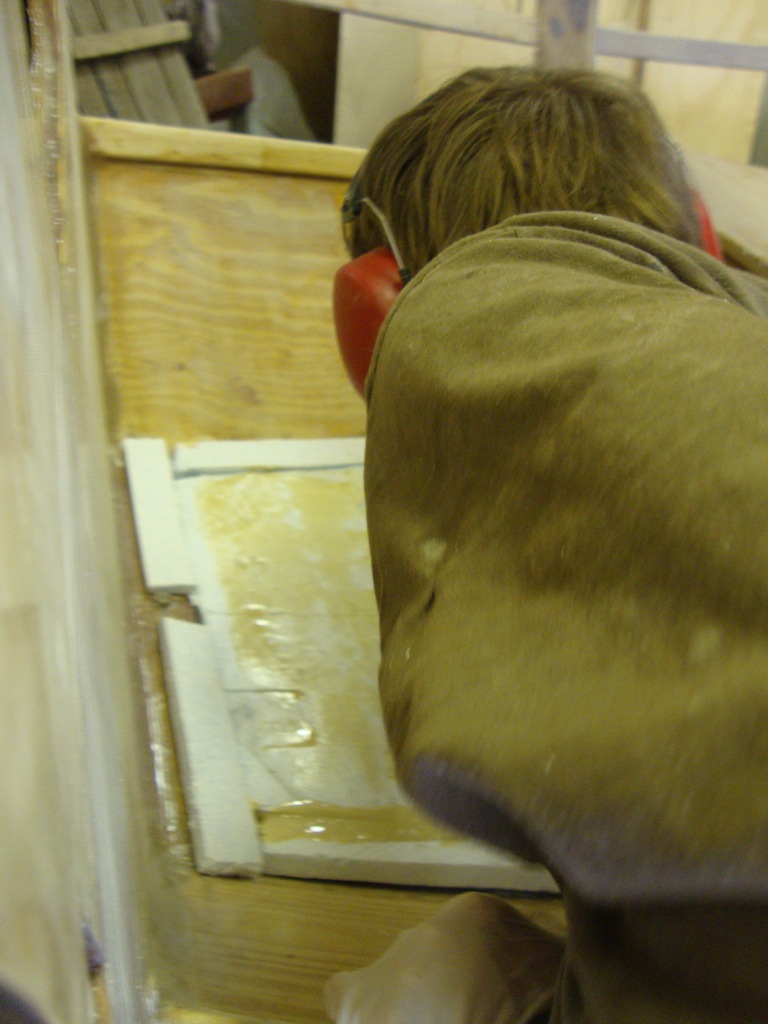
Joosep pouring the expanding foam onto our last bit of double floor between the cabin and watertight compartment. Speed of action was of greatest importance here, as the foam expanded fast.
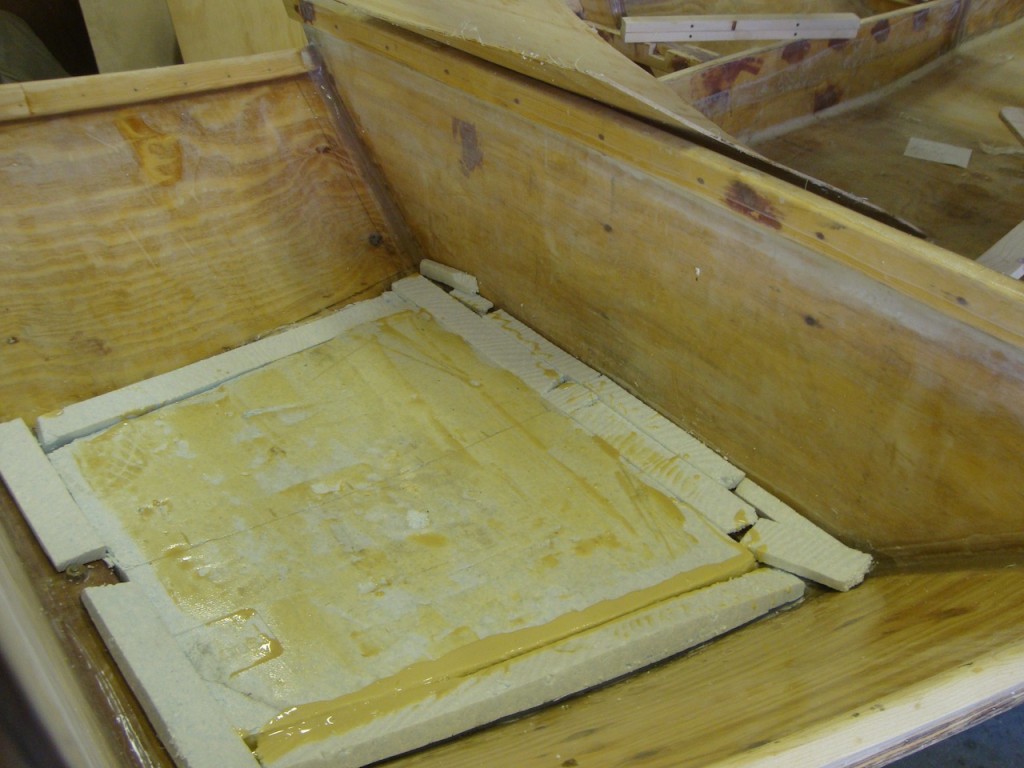
Before adding the weights and plywood to the intermediate cabin section. In theory, this is the room for storing water, straight under the mast.
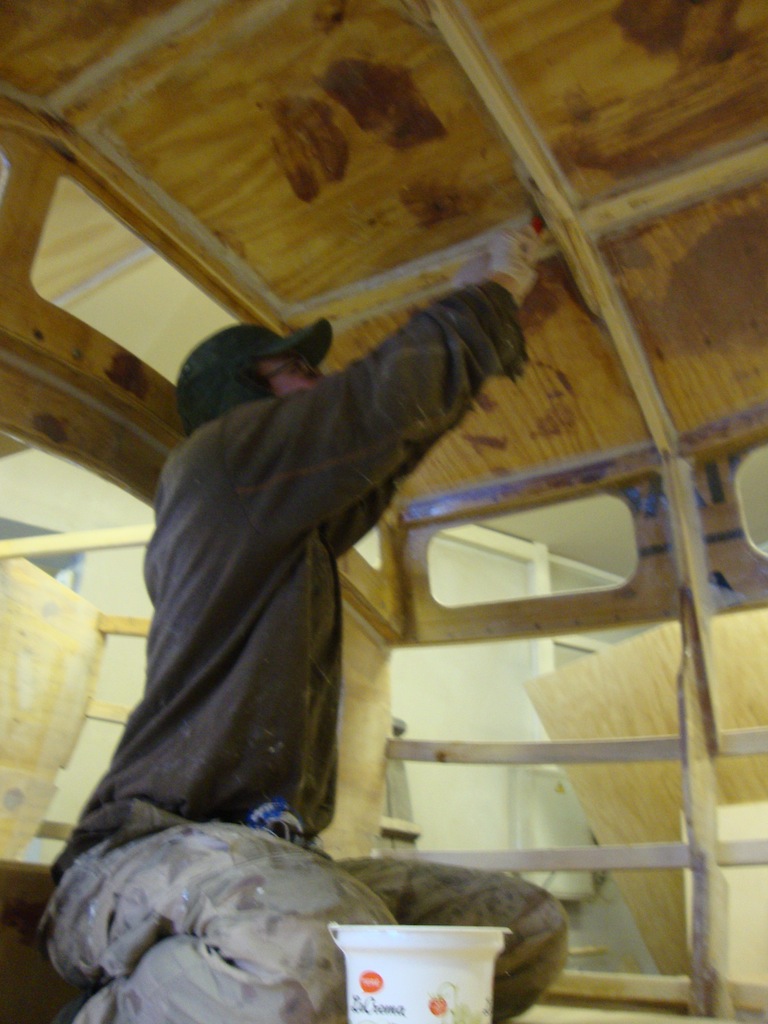
Joosep testing the patience of his nerves: glassing the cabin roof from the inside. So, another lesson learned: this should have been glassed forehand. Now it was a pain.
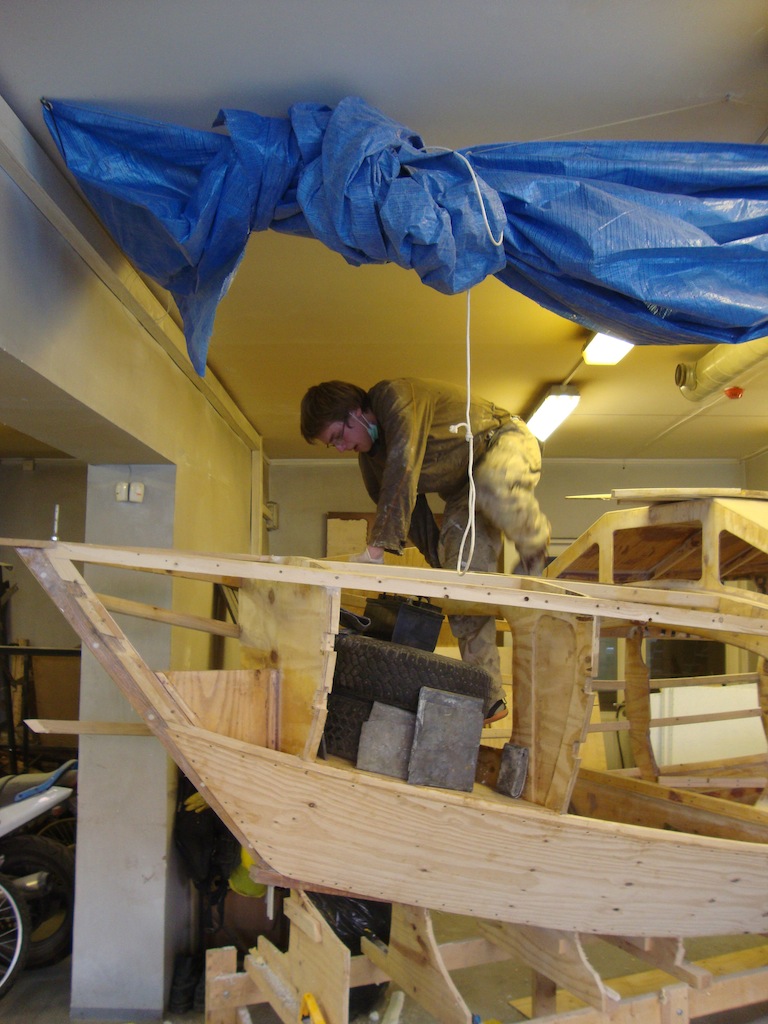
Fine weight system for putting pressure on the buoyancy compartment plywood as the foam expanded underneath.
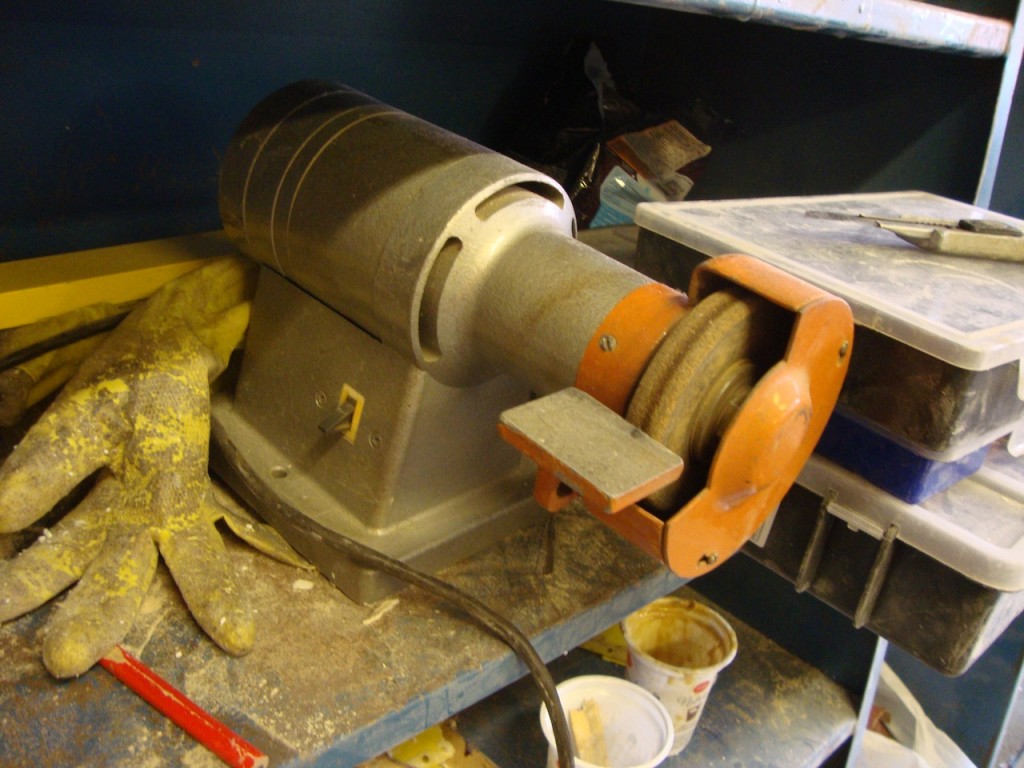
A new friend of the chisel, kife and hand plane. They are not dull anymore, sharp like the finest minds.
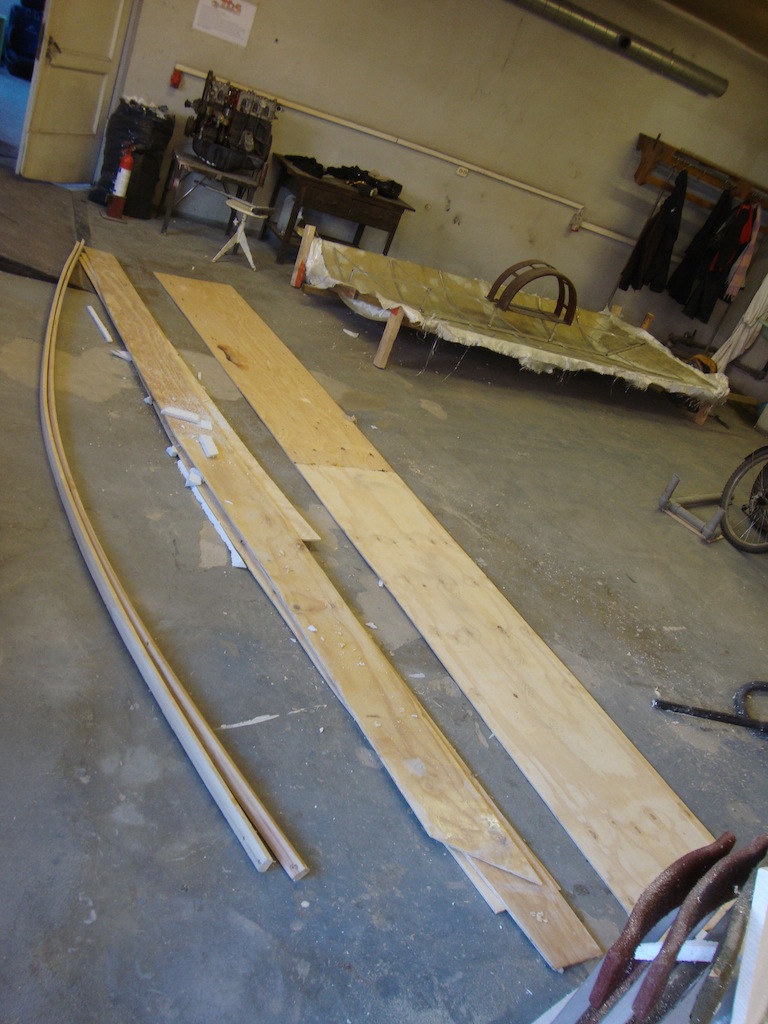
Our planks, stringers and in the back an airplane wing being built our hosts, the Technics club of the University of Life sciences.
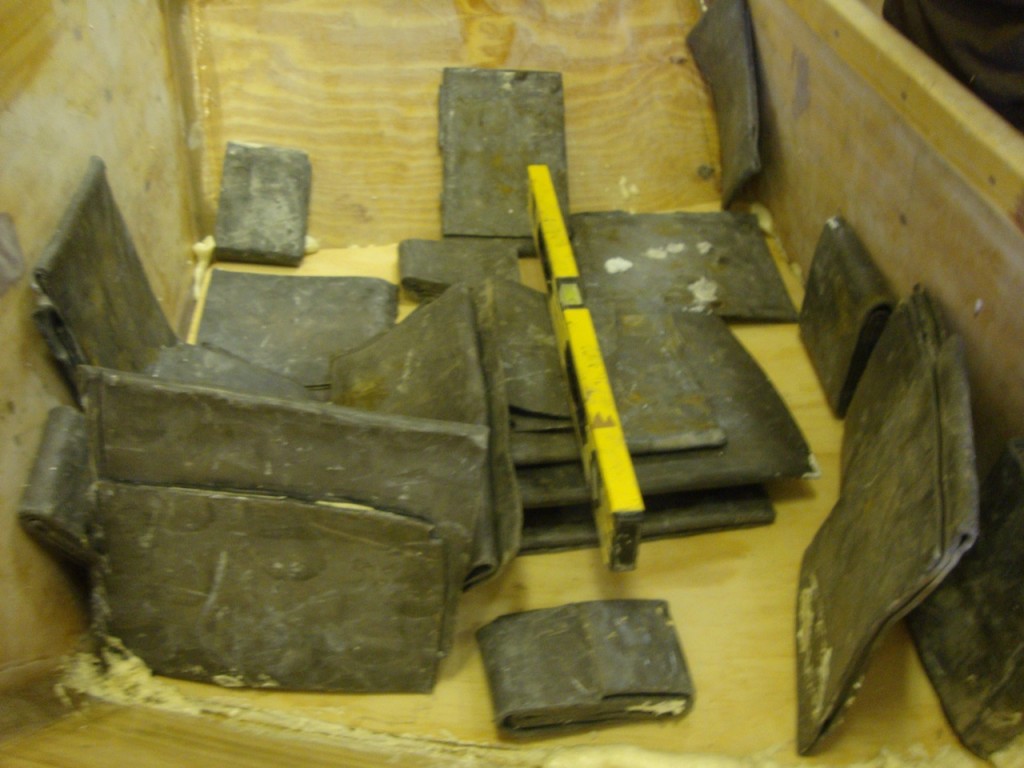
Just to check whether the weight lead is level or not. A high degree of perfectionism on not that high tech double floor.